General
Power electronics are a very fast-growing market segment, driven largely by rapid advances in e-mobility and renewable energy. In order to provide higher power density, higher efficiency and longer service life while lowering manufacturing cost, higher operating temperatures are one of the demands on the packaging technology, especially for latest-generation wide-bandgap semiconductor materials such as SiC and GaN with their high switching frequencies and low switching losses.
Soft soldering is the conventional die-attach process for power semiconductors but it suffers from several disadvantages such as susceptibility to creep deformation and, consequently, low reliability.
Operating temperatures beyond 250°C cannot be handled by solder connections.
The most widely adopted technology alternative is sintering with interfaces based on silver or copper.
Their temperature stability is excellent; at the same time their high electrical and thermal conductivity thanks to the very thin interface layer offers the advantage of superior cooling and lower thermal losses.
Silver sinter pastes can be used in high-pressure or low-pressure sinter processes, and they can be processed by TRESKY die-bonding equipment in very similar ways to conventional solder pastes. In addition, Die Transfer Films can also be handled in our machines.
There is a variety of processes for different sinter material combinations that have been developed over the years on TRESKY die bonding equipment.
Download
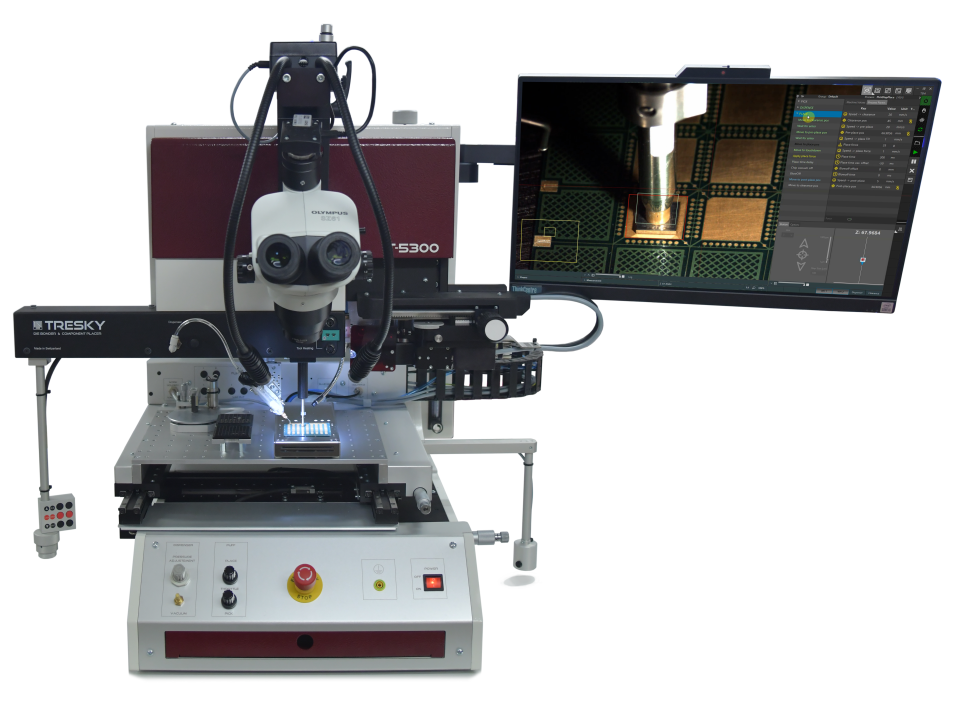
Low-Pressure Sinter Pastes
For low- or no-pressure sinter pastes, a two-step process is often used. First, the paste is applied to the substrate by a dispensing or screen-printing step. The die-bonder Model T-5300 then picks up the die, either from a waffle or gel pack or directly from a wafer, and places it into the sinter paste bed at a defined low force while the bond tool is heated to a programmed temperature of around 200°C for a short time to tack the die to the substrate. In the second step which can take much longer, the parts undergo an oven cure with a defined temperature profile and the microscopic metal particles fuse together in a controlled diffusion process, creating a powerful and durable bond.
In cases where the cycle time is not critical, the process can be simplified and carried out entirely in the die bonder. In addition to the heated bond tool, the substrate holder can also be heated with programmable temperature profiles to provide excellent process stability.
High-Pressure Sinter Pastes
The alternative process works with high pressure and is typically executed in a single step and at shorter cycle times. It uses high-pressure sinter pastes where the entire process takes place in the bonder. Here, pressures of 10 MPa and higher are employed at typical temperatures of 230°C for several minutes. The bonder can apply programmable forces of up to 100N on the T-5300 or 500N on T-3000-PRO, providing the required pressure for chip sizes up to about 7x7mm2. Higher temperatures up to 400°C are also achievable for different types of sinter paste, all with programmable temperature profiles in both the bond tool and the substrate holder.
A more recently developed technology uses Die Transfer Films instead of sinter pastes. They are readily handled by our die bonders in a manner similar to flux dipping of dies. The die is first placed onto a Die Transfer Film preform of the proper size. The film is then peeled, together with the die, off its support before placing it on the substrate, again with programmable force and temperature to tack it into position.
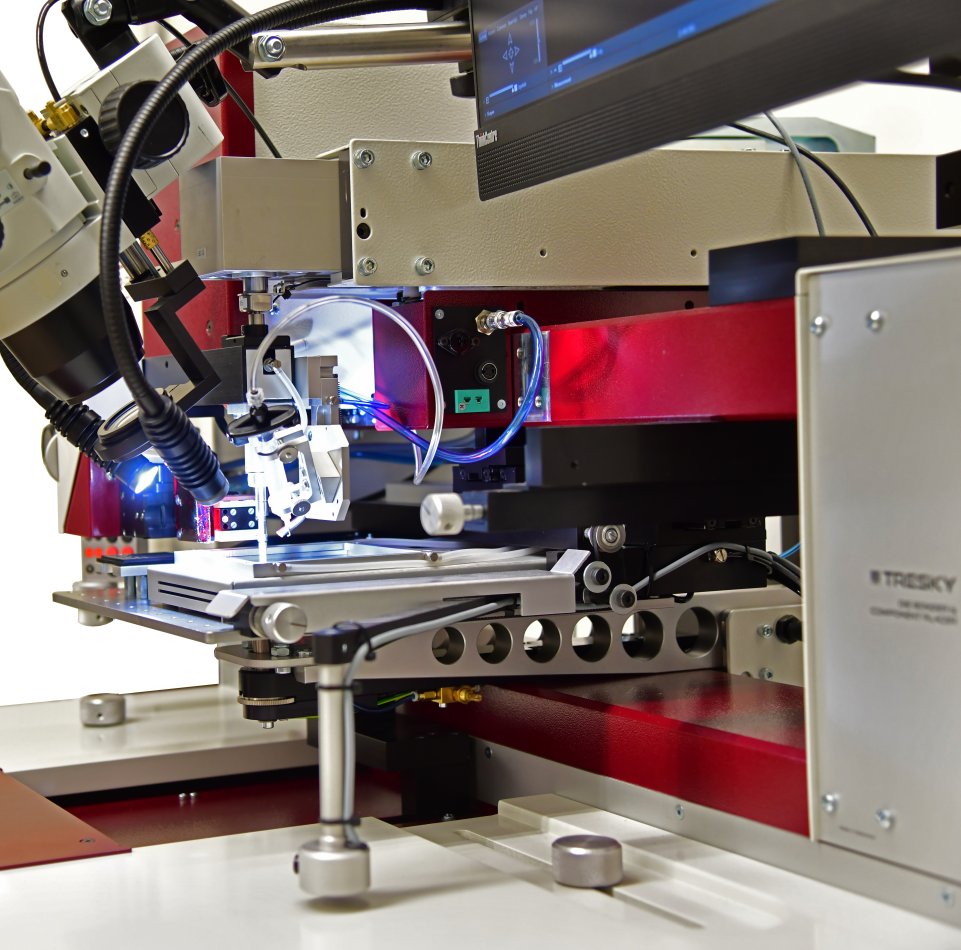
Other Sintering Systems
There are other uses for sintered interfaces on top of the semiconductor die, not only on the bottom side. Semiconductors operating at higher temperatures are preferably contacted with copper wires because aluminum wires as used conventionally suffer from much poorer reliability at the desired operating temperatures. The chief drawback of copper wires, however, is that they are much harder than aluminum and subject the die surface to far higher mechanical stress during wire bonding, again resulting in lower reliability. A newly developed, attractive way out is a mechanical bond buffer layer made out of copper with an applied silver sinter layer. This is placed on the die by the die bonder as an additional layer and is sintered simultaneously with the die to the substrate in the same process.
Any questions or interest in a online product demonstration?
Fabio Cocca - your sales contact at Dr. Tresky AG would be happy to talk to you personally. Give him a call or simply use our enquiry form.
+41 44 772 19 41
Please note our privacy policy.